Innovative Amino Acid Production from Agricultural Biomass
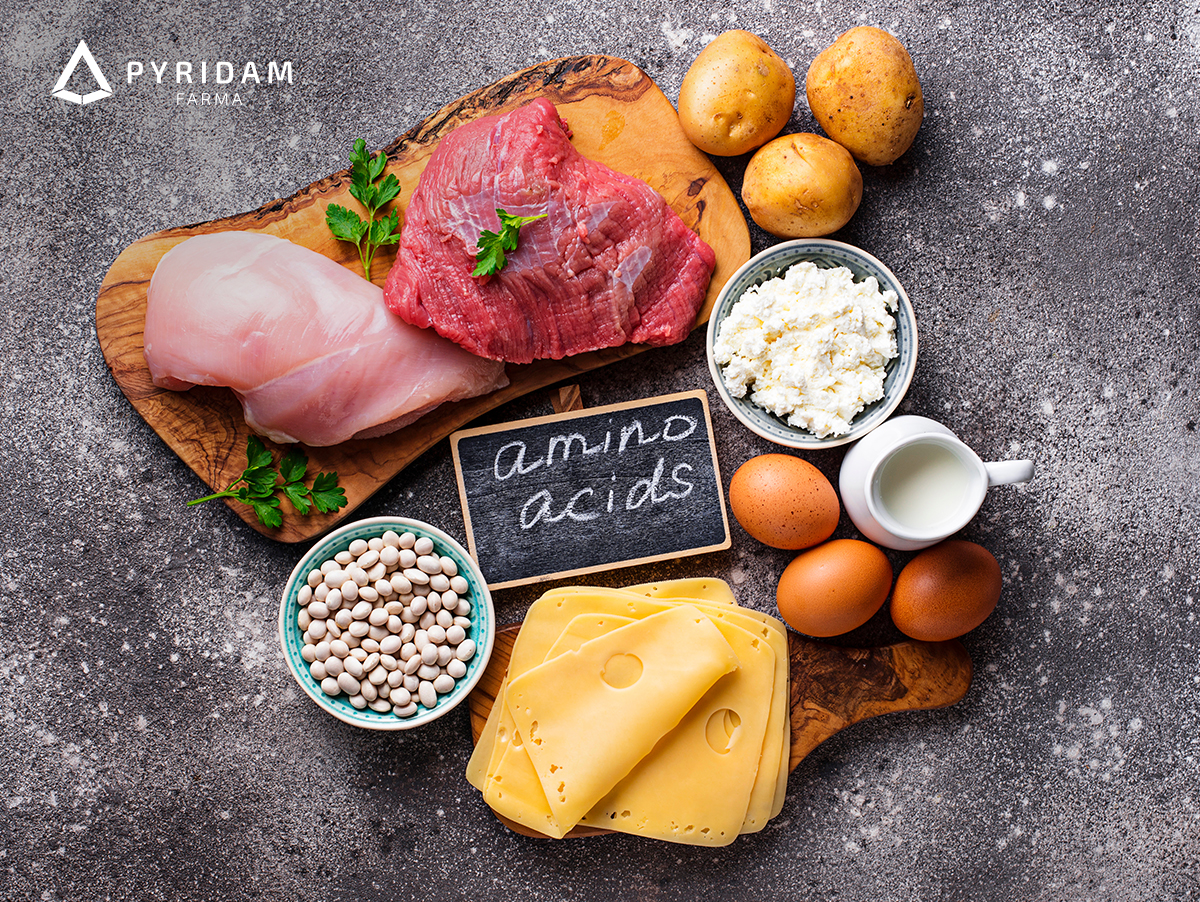
As the world’s population grows, the agricultural sector continues to expand to meet the growing demand for food. Currently, around 23.7 million tonnes of food is produced every day from the agricultural sector. By 2050, food production is expected to increase from 8.4 billion tonnes to 13.4 billion tonnes per year. However, this development of the agricultural industry has also led to an increasing amount of waste being generated.
Agriculture in Indonesia and Malaysia produces large amounts of waste that needs to be managed to address environmental issues. These wastes generally have high starch and lignocellulose content, and have the potential to be utilised for the development of value-added products, such as amino acid production. Traditional methods often rely on expensive commercial enzymes to convert biomass into fermentable sugars for amino acid production. An alternative, consolidated bioprocessing, enables the direct conversion of agricultural biomass into amino acids using selected microorganisms. This review provides a comprehensive assessment of the potential of agricultural biomass in Indonesia and Malaysia for amino acid production via consolidated bioprocessing, through the use of suitable microorganisms.
Consolidated Bioprocessing (CBP) is a process that combines enzyme production, saccharification and fermentation into a single step. This approach reduces costs and increases productivity, making it popular for producing low-cost and value-added products. However, finding microbes that can perform all the necessary processes in one step is a challenge. Often, bacteria are the best choice as they can produce the required amino acids and enzymes.
Different types of bacteria have different capabilities. For example, some strains of Escherichia coli can make methionine and tryptophan, while Bacillus subtilis is able to make lysine. Optimising fermentation conditions, such as temperature and agitation, is also important to improve efficiency.
The use of processed raw materials, such as maize stover and pineapple plant stalks, can also help make the process more sustainable. This highlights the need for innovation and optimisation to meet the growing demand for low-cost and sustainable production. Different types of bacteria, including E. coli, B. subtilis, Corynebacterium glutamicum and Pediococcus species, have unique metabolic capabilities that can adapt to different feedstock substrates.
The flexibility of bacteria to use different feedstocks, such as glucose, molasses, soybean meal, corn stover, and pineapple plant stalk, supports the flexibility of CBP in amino acid production. However, the amount of amino acids produced varies between microbial strains and feedstock substrates, so process optimisation is important. In a study conducted by Li et al. (2022), starch was used as the main feedstock for l-lysine production through genetic engineering of C. glutamicum strain KT45-6S-5, which produced 23.9 g/L lysine.
The use of microorganism co-cultures involving B. subtilis, C. glutamicum or E. coli for amino acid production from agricultural biomass shows great potential in improving process efficiency and yield through consolidated bioprocessing. However, research is needed to study its feasibility and understand the benefits and limitations of co-culture systems in the amino acid industry, as well as their optimization for process improvement.
This article contributes to the advancement of sustainable amino acid production methods using agricultural biomass specifically through bioprocess consolidation, waste reduction, and improved environmental sustainability.
Keywords: Amino acid production, agricultural waste, consolidated bioprocessing
Source: Pei-Hsia Chu, Mohd Azwan Jenol, Lai-Yee Phang, Mohamad Faizal Ibrahim, Purkan Purkan, Sofjan Hadi, Suraini Abd-Aziz. Innovative approaches for amino acid production via consolidated bioprocessing of agricultural biomass. Environmental Science and Pollution Research, 2024. Vol 31. Issue 21. https://doi.org/10.1007/s11356-024-33534-0